Some eight years ago the Via Flaminia (rally) was born out of love for Italy and classic cars. Last year, Bart Kleyn set out to organize an all pre-war rally. He was hoping for an Alfa 6C or a Lancia Lambda but none entered.
He was resigned to being happy with the registration of Speed Sixes and Lagonda’s when David and Karen Ayre entered their 1907 Itala. Then came another break…being a passionate of Lancias, Kleyn was thrilled when Daniel Ward registered his 1914 Theta; not just some old banger, but one which had done the 2010 Peking to Paris (9317 miles in 35 days over the harshest terrain one can imagine).
He offered to us this short personal account of the story of the Lancia Theta as it sped through the Mongolian desert. If you ever wondered how these guys make it through the hinterlands of Mongolia with an old Italian car, read on. For more about the actual Peking to Paris Itala, click here.
Here is Daniel Ward’s account:
We bought the Lancia Theta in a Bonhams sale in London in March 2004 sometime after the death of its previous owner, Oliver Gray, who had restored it the first time around. It had latterly been used by a garage in Plymouth (U.K.) as a pick-up truck for breakdown recovery with a crane on the back of it. Grey had built a box-like rear body behind the front seats which was not very pretty, called a Barnstaple Tourer. The front seats, scuttle and bonnet were all original. But the car was mechanically very tired, the cylinder block was cracked internally with water leaking into the combustion chamber on #2 cylinder and the brakes and clutch were extremely worn making the car very difficult to drive safely.
I had wanted the car from the first time I saw it twenty year before that. It was on one of the first Veteran Car Club Rallies we had ever been on. The Rally was a re-enactment of the 1904 Light Car Trials centered in the beautiful City of Hereford. It was a week long event around all of the cider farms in Herefordshire – every one of them gave us free cider and so we had to take it in turns to drive in the afternoons as we drank so much at lunchtime. I even fell out of the car one afternoon–fortunately I wasn’t driving at that time. We were driving a 1903 14 Hp. 4 Cylinder Vinot et Deguingand which we had just restored. although it was a car our father had bought in 1946. It is a good car and pretty competent up hills and on the flat, but we were continually being overtaken at high speed by this blasted Lancia Theta. Not only did it pass us going up hills, but is was accelerating all the time – I couldn’t believe what a good car it was. I never thought then that I would get the chance to own it.
After we brought the Theta home, we used it a few times but then parked it up because it obviously needed a full and expensive mechanical overhaul – and being a Lancia it was quite a complicated project to tackle. It was not until I decided to enter the 2010 Peking to Paris Rally that we decided to use the Lancia. I had done the 2007 Peking to Paris in our 1908 Talbot 4F so knew what to expect and thought it was the excuse we needed to renovate the Theta.
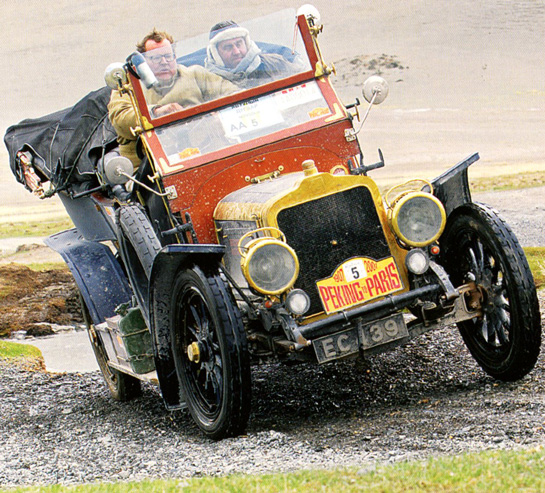
In 2007 Ward and co driver David Ingle entered the Peking to Paris in this 1908 5.3 liter Talbot seen here in the Gobi Desert. Photo by Gerard Brown, from the book 'Peking to Paris'.
So we did a complete mechanical overhaul and replaced the old
reproduction Barnstaple Tourer rear section of the body with a boat tail tourer style which looks more exotic. We spent a fortune on the engine and repairing the cylinder block, the gearbox, back axle and when we had finished it ran beautifully. The car pulled like a train and if anything is under geared,as it stills accelerates up any hill – it would still make a very good break-down tow-truck! Going down the other side is a slower affair with only 2 wheel brakes.
It went extremely well on the Peking to Paris – the only thing that continually gave us problems was the front stub axles. The problems weren’t small ones either, because it kept snapping the thread off the end of the stub axle, and every time that happened the front wheel would come. This happened five times – and off course every time the front wheel comes off the car hits the road and you loose the ability to steer it when it veers off in the direction of whichever side the wheel has come off.
Fortunately the first four times this happened we were on the desert tracks of Mongolia but the final time was on a rough road in Russia, we were doing about 60 kph at the time and the car careered into a bank, burying the front axle into the dirt, bending it and the front dumb iron. When the car came to a halt and we got out we found that the exhaust had set fire to the dry grass under the car and of course we couldn’t move it because it was on 3 wheels and buried in a bank! Mercifully we managed to put the fire our with our handy extinguisher or it would have been curtains for the whole project.
We still had two further problems – getting the car out of the dirt onto a flat area where you can jack it up and then, not least of your worries – finding where the blasted wheel has gone to in dense scrub. That took about an hour of searching amongst some very spiky thorn bushes.
So what was causing this very inconvenient and rather dangerous mechanical failure? The first time it happened was when we entered Mongolia on the second day across the desert – which is like driving across a ploughed field for hours on end – we put it down to metal fatigue in the nearly 100 year old stub axles which were under extreme strain given the big load the car was expected to carry over the appalling terrain.
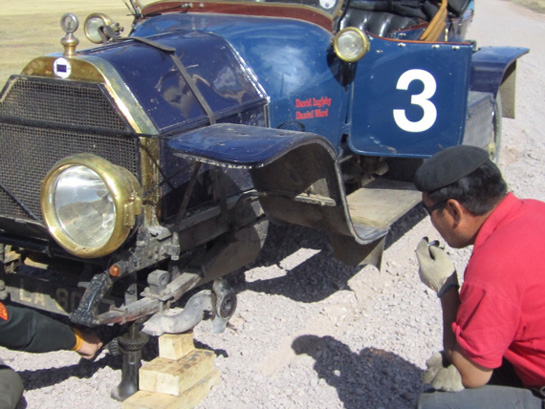
Closer inspection reveals the same problem, which turned out not to be the fault of Lancia or its designer. Photo courtesy David Ayre.
The only way to mend the broken stub was to bore it out of the wrist of the stub axle with a 2 inch drill from the rear of the forging. Then we turned up a new stub, using whatever steel was in available in the very poorly equipped workshops of outer Mongolia and then finding a big enough electric arc stick welder to weld the new stub into the old wrist using the sexy welding rods we had brought with us -this is not a repair you would ever even dream of doing in Western Europe – but when needs must – the devil drives, as they say.
The repair was successful but having done one side, the other did the exact same thing the day after so this made us think our theory was right, that the old metal was fatigued. So we did the same thing again. But then, 2 days later and after more punishment, the first repair broke again and the day after that the other side did the same thing – we put this down to the fact that we didn’t know what the quality of the steel was that we had used in the repair – they were just bits of rusty old bar steel we had found on the floor of the filthy old workshops we had been using.
In Mongolia you are very lucky to find any steel at all and they certainly hadn’t got a clue what the quality of the steel was – and that is assuming you might now enough Mongolian to even ask! By this time , we had been sent a pair of replacement stub axles out from the U.K. by the great kindness of Tim Jones and Nick Benwell, two Lancia Theta owners who knew of our troubles and actually took a pair off Tim’s car and air freighted them out to meet us in Almaty.
But by this time we had had five failures of which one was actually due to poor welding which we rectified quite easily by welding deeply from the front and rear of the stub. But we decided on the next rest day, with the help of David Ayre (Itala) to have another good hard look at the problem – were we right about metal fatigue? – in a “Eureka” moment we decided to check the positioning of the bearings in relation to the hub by measuring the distances accurately.
You cannot see where the bearings sit because they are inside the hub and you just don’t expect them to be incorrectly spaced, but when we measured the positioning accurately the answer was plain to see, the outer, small bearing was 18 mm. too far from the inside of the hub and locating on the smallest diameter part of the stub axle. This greatly amplified the load on the stub axle at its weakest point – that is what was causing the failures.
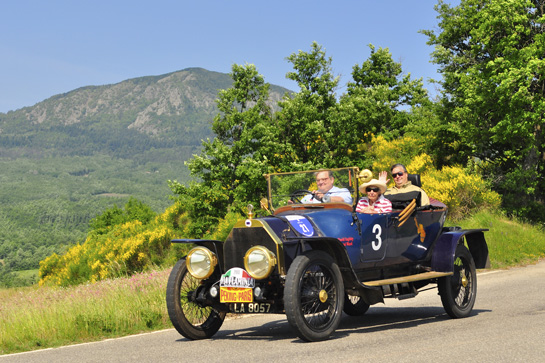
The stub axle problem was long resolved by the time of the 2011 Via Flaminia and Ward was able to enjoy a trouble free run in the sun. Photo Via Flaminia.
We also realized that the wheel bearings had been changed at some point, by someone unknown from ball race bearings to modern taper rollers and when that had been done the new bearings were fitted using the old spacers for the ball races – which, being self centering, they didn’t need anyway. This was locating them too far out. All very well knowing the cause but that then gave us another problem – where to find a machine shop that would be open at 2.00 pm on a Friday afternoon in Samarkand – a Muslim Country. This we did when we found that the repair shop for a local bus company was still open and I managed to persuade the elderly machinist to give up his Friday evening prayers, no doubt risking untold damage to his sole in the future, in return for a fistful of the mighty dollar. Invariably these have an electrifying effect in the Oriental parts of the globe in overcoming difficulties of a Spiritual nature. And then we had to find a big enough lump of steel to make the inner hub with – more dollars etc. then a new set of taper roller bearings as we had destroyed all of our spares – these actually were found in a splendid open air car market where there were dealers with piles of secondhand Russian bearings for sale – again all is ok and possible when needs must.

According to Ward, the Theta is very powerful, with a 4.9 liter engine. Photo courtesy Via Flaminia.
And thus, finally we got to the bottom of our stub axle problem – it was absolutely nothing to do with Lancia design and everything to do with a botched latter day modification.
All in all, the Theta is a really wonderful car – technologically advanced for its day , fitted with electric lighting and a self starter as standard in 1914 and with bags of power from its very compact 4.9 Litre engine, it is a joy to drive – to the ends of the earth, if that takes your fancy.
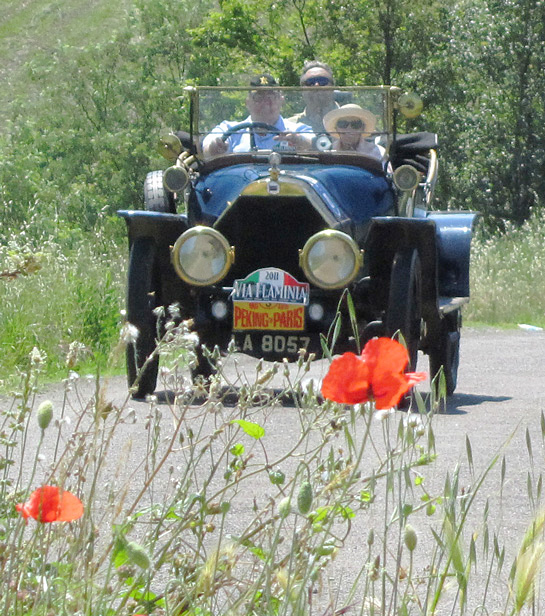
Via Flaminia tour takes routes that are visually stunning and fun to drive, as the Theta finds out. Photo courtesy Via Flaminia.
If, after reading this epic tale you would like do a rally but are not really convinced the Peking to Paris is your thing, then consider the Via Flaminia Pre War If you do not have a pre war car then you might want to go for the classic editions in June and September
To Daniel Ward , Delighted to see the Lancia theta restored , my god that car brings back lovely memories , it was Mum & Dads favourite car , yes slightly undergeared , but up a hill !! . kind regards , Allan Gray