In Part 1 Restoration expert Alex Bacon begins a project to create a 1950s era-Sports Racer based on Alfa 2600 components. After completing the chassis the body is now taking shape.
Photos courtesy Alex Bacon
Next came a classic use of CAD-derived inspiration; CAD, meaning Cardboard Aided Design, in which cardboard templates are cut for front fenders, hood, cowl, doors, rear fenders, and trunk to quickly simulate the body shape. The cardboard templates were revised multiple times until a satisfactory shape was achieved. Plywood forms fashioned from the cardboard templates were installed to provide references for body panels and the locations for the small diameter tubing to support them.
The front-end design comprised complex, compound curves that did not lend themselves to representation in cardboard or plywood, so a solid block of foam was installed. Over many days, the foam was sculpted into the final form. The door frames were built from small diameter tubing, hinges fabricated, and latch mechanisms based on Italian units of the period were designed and constructed. Now, the chassis could be rolled out of the shop into the sun, and the overall shape and proportions appraised. It was beginning to look like a car.
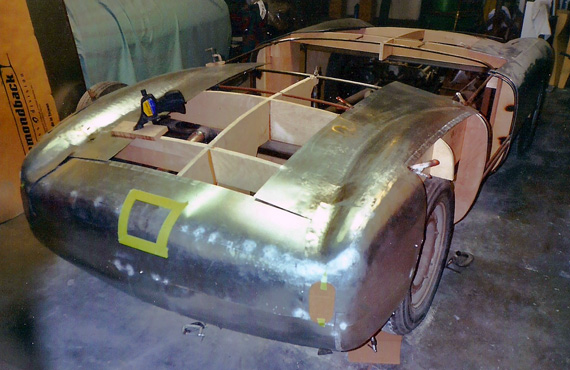
Cut, shape, hammer and weld the aluminum pieces to follow the wooden buck. Sixteen separate sheets were needed just for the rear section.
Months of metal work remained, shaping sheet aluminum panels over bucks, using an English wheel, fitting and revising and fitting, again. The front of the body required 16 separate pieces of aluminum and the front fenders 4 pieces each to complete the forward body section. The aft body section required 12 pieces for the rear and 4 pieces for each fender. The rockers were 6 pieces on each side. For the hood, trunk and each door skin, single, formed sheets of aluminum were used. Just as in sports racers of the period, no provisions for bumper attachment were considered.
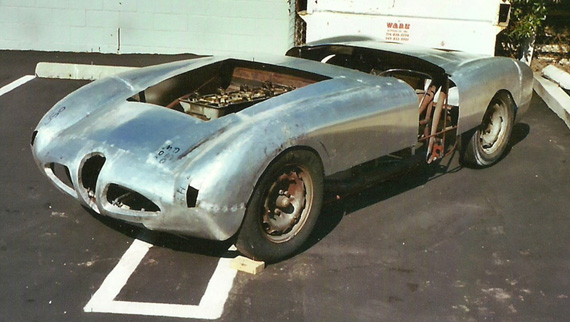
Now looking like a real car, the Alfa is brought outside to get a better view and judge overall proportions.
Now that the chassis had a skin, decisions about fender radius, the location of grille openings, headlight and taillight positioning could be made. Careful study of the Colli-bodied Alfa Romeo 6C3000CM provided the design for the taillights, the size and shape of the grille openings, headlight buckets, and rear license plate frame. A great deal of time was spent conceptualizing the execution of each piece, experimenting with proportions and fit, and selection of material. Every piece on the car needed to reflect a cohesive theme, supporting the overall design vision, contributing to the aesthetic of the original concept, and keeping with the period correct interpretation. Nothing about the car could look out of scale, out of place or period incorrect; no detail could corrupt the authenticity desired for the completed project.
Next came fabrication of the transmission tunnel, dashboard, trunk floor, fenderwells, foot wells, and engine bay sheet metal, all formed from aluminum and, like the body, gas welded. At the end of two years, the basics were complete and the body could be removed section by section, and the chassis disassembled and prepped for painting.
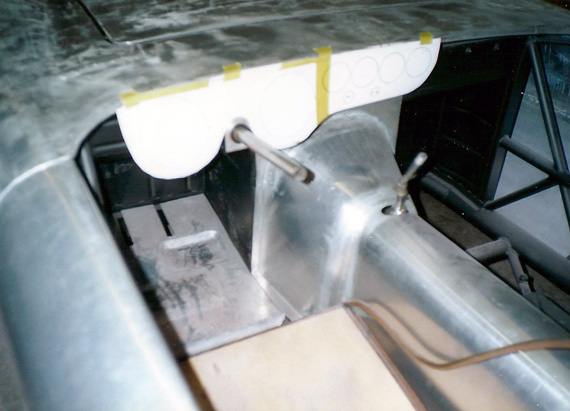
After the main body panels were fabricated work began on the inner panels. The gearbox had to be internally modified to place the shift lever in a comfortable position, due to the rear placement of the six cylinder engine.
The chassis was painted matte black and the engine was rebuilt, with performance upgrades including built up and profiled camshafts with higher lift, Toyota valves and dual valve springs, custom valve guides, high compression pistons, ported and polished head, and triple Weber carburetors. An exhaust header was fabricated and the head flange match-mated to the exhaust ports. The transmission was disassembled and inspected, worn parts replaced, and the top of the transmission tailpiece was cut off and a machined plate welded in place. The rearward location of engine and transmission necessitated fabricating complex, shifting linkage using an Alfa Romeo 105 series selector finger and slider to locate the shift lever in a comfortable, driver-friendly position. The pedal box and pedals, with lightened footpads, were fabricated, and brake and master cylinders installed utilizing original, remote reservoirs. Solid brake lines were routed and installed and a simple electrical schematic for the wiring harness was created.
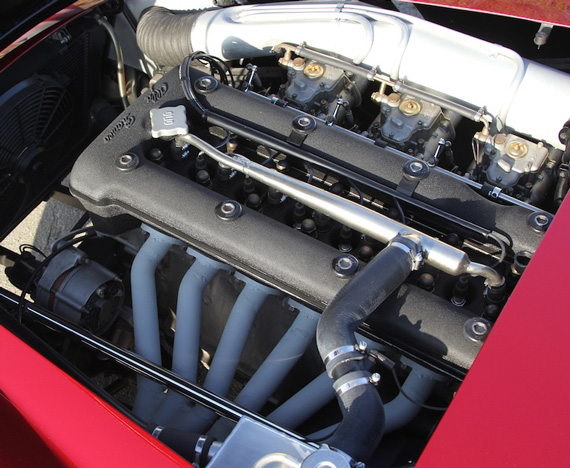
Note the elegant fabrication of a vintage era water inlet as well as the fabrication spark plug wire feeder, and the intake system feeding the triple Webers.
All electrical components, like turn signal flasher unit, relays for high/low beam headlight switching, electric radiator fan and horn, and the fuse block were located on a panel in the passenger compartment. A wiring harness of cloth-covered wire was constructed based on the wiring schematic and installed.
Now came consideration of the braking system. In order to fit knock off wire wheels with period correct 42mm hubs, reverse-laced, painted, not chrome, 16″ wire wheels were ordered from Dayton and fitted with 165×16 Avon 80 series tires. (Sports racers of the period rarely ran chrome wire wheels, due to cost, weight, and subsequent weakening of the spokes following the plating procedure. Magnesium wheels soon became the default choice for racing.) Polished Borrani-style knock-offs from England were acquired. Alfa Romeo calipers and rotors were machined to fit inside the diameter of the wheel rims, and all the front suspension and steering components were rebuilt with new bushings. Custom front wheel bearings were machined for the 42mm hubs.
The aluminum dashboard was painted in a hammered finish and instruments and switchgear were appropriated. To keep dashboard appearance authentic but the engine precisely monitored, modern VDO instruments for fuel level, water temp, oil pressure, and oil temperature were used with unique, silk-screened dials and hand fabricated bezels. Large diameter, Alfa Romeo speedometer and tachometer received unique, silk-screened dials and custom fabricated bezels as well so that all the instruments matched and retained the period correct appearance. Since a modern alternator assembly with an integral voltage regulator was used, rather than include an amp gauge, a warning light was placed on the dash between the original Alfa Romeo 2600 light switch and an illuminated, turn signal lever that was sculpted from a block of acrylic and then sand blasted to better infuse light.
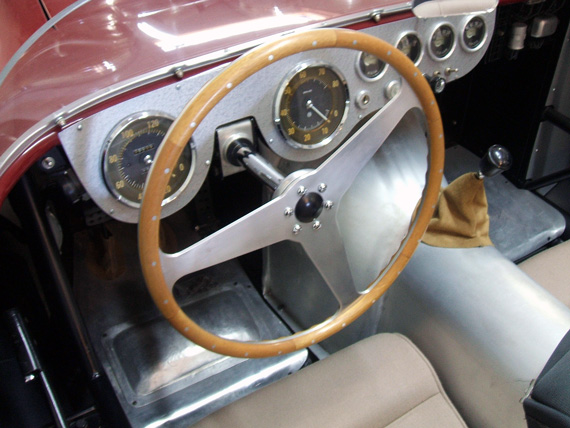
Tach and speedometer were also designed for a vintage, period appearance. The steering wheel is crafted from wood and aluminum.
To actuate the horn, a period correct Lucas push button was fitted at the left edge of the dashboard. Toggle switches control the fuel pump and electric radiator fan. A steering wheel frame was cut from a single sheet of heavy gauge aluminum, filed and sanded and polished, and the wood rim binding carved, bonded and riveted in place. Formula requirements for a World Sports Car Championship entry from 1953 to 1961 mandated a spare tire, so provisions were designed and constructed to secure a spare tire in the trunk above the fuel tank. In addition, to conform to the racing formula, passenger seating was required, but not the size of the passenger seating, so it was decided to significantly shorten the passenger footwell and leave the oil filter of the 2600 engine in its original location.
Next week: Final details and driving impressions
A true labor of love, great craftsmanship. Which intake did you use? Modify the Solex one, fab one or a rare factory Weber manifold? Thanks
The author spoke with Alex Bacon over the weekend about the intake manifold on his sports racer. Alex designed and fabricated the manifold for the Webers on his engine.
Ed.